(сокращенный вариант)
Известный факт , что взаимозаменяемые подшипники
качения для удобства их сборки на конвейере выполняют с расширенными
примерно вдвое радиальными зазорами. Как объясняют производители
, это делается вынужденно в ущерб долговечности подшипников.
Институт подшипниковой промышленности провел при постоянном
нагрузочном и скоростном режимах стендовые испытания цилиндрических
роликовых подшипников типа 12208 с различными величинами радиальных
зазоров. Испытания показали, что подшипники с радиальными
зазорами 15-30 мкм (что соответствует нормам для невзаимозаменяемых
подшипников) имели среднюю долговечность 4400 часов, а у подшипников
с радиальными зазорами 20-55 мкм (что соответствует нормам
для взаимозаменяемых подшипников) средняя долговечность была
равна примерно 2100 часов, что меньше более чем в два раза
. Подшипники с допуском на угол конуса на наружных и внутренних
колец 0-1 мкм имеют среднюю долговечность более чем в 2 раза
больше средней долговечности подшипников с углом конуса по
действующим нормативам 0-2,5 мкм. Это свидетельствует о том,
что можно смело производить накатку абсолютно новых взаимозаменяемых
подшипников составами с КЕРАМИДАМИ не дожидаясь их обкатки.
Накатка КЕРАМИДАМИ уменьшит радиальные зазоры и осевую игру,
приведет их к приемлемому значению, т.е. фактически устранит
некоторые недоработки производителей подшипников. Стоимость
устранения этих недоработок обычными методами подшипниковым
заводам обошлась бы очень дорого, что привело бы к большому
, возможно не оправданному , подорожанию самих подшипников.
В практике подшипникостроения 80-90% от общего объема выпускаемых
изделий - взаимозаменяемые подшипники с пониженной степенью
точности, т.е. нуждающиеся в обработке КЕРАМИДАМИ сразу после
их изготовления. Большое влияние на долговечность подшипников
оказывает состояние поверхностного слоя рабочих поверхностей
подшипников. Шлифование , полирование и доводка в значительной
степени определяют эксплуатационную долговечность подшипников.
Повышение степени точности изготовления тел
качения (шариков и роликов) увеличивает долговечность подшипников.
Например, применение в подшипниках качения шариков второй
степени точности вместо третей повышает долговечность всего
подшипника на 30% и благоприятно отражается на точности вращения.
Зерна состава типа КЕРАМИД, накатываясь на дорожки, шарики
или ролики уменьшают их шероховатость, заполняя впадины и
перекрывая выступы шероховатости, не повторяя их рельеф, как
бы повышая эквивалентную степень точности дорожек качения
и тел качения, существенно увеличивая продолжительность работы
подшипников до отказа.
Расчетный ресурс работы подшипников может
быть обеспечен только при условии соблюдения надлежащего режима
смазки и теплоотвода. Но чрезмерное скопление смазочного материала
ухудшает работу подшипника, ибо на ее перемешивание затрачивается
избыточная энергия , переходящая в тепло , что повышает температуру
подшипника и узла в целом. В таком случае подшипник при вращении
ломает и перемалывает “структурный каркас” консистентной смазки,
вызывая отделение из мыла жидкой составляющей , т.е. смешанного
с ним минерального масла. Последнее в этом случае легко вытекает
сквозь уплотнения , засыхающее мыло образует твердеющий “шлам”
, не обладающий необходимым смазывающим свойством. Применение
смазок содержащих КЕРАМИДЫ позволяет уменьшить количество
закладываемых консистентных смазок, уменьшив расход электроэнергии
на перемалывание смазок, понизить температуру узлов механизмов.
Кроме того , КЕРАМИДЫ, являясь сухой смазкой, допускает применение
не только любых смазочных материалов (“какие есть”) , но может
обеспечить работоспособность подшипниковых узлов без смазки
т.е. насухую. Смазка является средством доставки в смазываемые
части КЕРАМИДА. После накатки КЕРАМИДА на трущиеся детали
необходимость в консистентной смазке отпадает. Хотя, реально,
в производстве ее из подшипника нет смысла удалять.
Во многих случаях подшипники должны работать
при высоких скоростях , создающих в рабочих деталях (телах
качения и наружных кольцах) напряжения , превосходящие те
, которые вызываются на внутренних кольцах приложенной внешней
нагрузкой. Не только в узлах высокоскоростных шпинделей ,
газотурбинных двигателей и авиаагрегатов, но даже в буксах
железнодорожного транспорта более легкие подшипники работоспособнее
и надежнее, чем тяжелые. Явления , связанные с разрушением
подшипника при высоких скоростях , прогрессируют примерно
в линейной зависимости от угловой скорости и габаритных размеров
подшипника. Разрушение в данном случае происходит из-за выдавливания
смазки между телами качения, наружным кольцом и сепаратором,
увеличения контактных напряжений. Создаются условия сухого
или полужидкого трения в связи с чем поднимается температура
подшипникового узла. Для оценки быстроходности был предложен
параметр d*n мм*об/мин=const. Этот параметр не учитывает коэффициент
трения между частями подшипника , хотя известно , что количество
тепла , выделяемого в подшипнике , в результате потерь на
трение, рассчитывается по формуле;
W=P f V / 427 ккал/сек
то есть количество тепла прямо пропорционально
коэфф трения. Уменьшая коэффициент трения, что позволяет сделать
применение КЕРАМИДА , улучшаются тепловые характеристики подшипников.
Это четко прослеживается на практике, когда после обработки
составом температура подшипникового узла падает с 70-80 градусов
до 30-40 градусов. Состав предохраняет части подшипника от
сухого и полусухого трения в моменты когда отсутствует смазка
или ее количество недостаточно для жидкостного трения. Это
может наблюдаться не только при больших скоростях вращения,
отсутствии смазки из-за несвоевременного проведения технического
обслуживания подшипникового узла, но и в моменты начала работы
механизма. Когда механизм, содержащий подшипниковые узлы,
не работает , происходит выдавливание смазки между телами
качения и кольцами. В такие моменты коэффициент трения с обычного
0,001-0,002 повышается до 0,2 вызывая в некоторых случаях
(при больших статических нагрузках) холодное приваривание.
Применение смазок с КЕРАМИДАМИ исключает эту возможность,
так как сухая смазка КЕРАМИД имеет твердость на поверхности
обкатываемых тел около HRC 64 и не выдавливается даже при
нагрузках, которые способны разрушить тела качения.
“Следует отметить, что наибольшие касательные
усилия на контакте возникают перед срывом сцепления , а не
после начала скольжения или качения. По абсолютной величине
они непосредственно зависят от величины коэффициента трения
между контактируемыми поверхностями.” [“Подшипники качения.”
А.И.Спришевский “Машиностроение” стр. 272 ].
В результате контакта тела качения с неподвижной
поверхностью желоба и действия сил трения на рабочих поверхностях
возникает сложная система касательных усилий , замыкающаяся
в пределах зоны равной 3-4 диаметрам зоны контакта, и вызывающая
появление соответствующей системы упругих микроперемещений
и даже микропроскальзываний. Исследования показывают, что
перемещения на передней кромке в связи с изогнутостью контактной
поверхности под воздействием сил трения качения, увеличиваются
по сравнению со статическими на 40%, а на задней кромке уменьшаются
на такую же величину. Соответственно изменяются относительные
удлинения и растягивающие напряжения. Покрытые твердой пленкой
КЕРАМИДА детали подшипника частично защищены от такого воздействия
растягивающе-сжимающих напряжений самой пленкой, а значительное
уменьшение трения качения уменьшает эти напряжения до 3-5%.
Напряжения, возникающие на неровностях рабочих поверхностей,
могут значительно превышать напряжения сдвига, возникающие
на критической глубине под поверхностью контакта. Микротрещины
появляются почти сразу после начала работы подшипника. Края
трещины являются естественными концентраторами напряжений
и появление новых перенапряженных микрообъемов обуславливает
прогрессирующее развитие усталостной микротрещины с соответствующим
перераспределением напряжений (перенос напряжений на соседние
участки) в рабочем сечении детали, которое заканчивается хрупким
разрушением материала. По мнению С.В.Пинегина [“Контактная
прочность в машинах” “Машиностроение”] процесс образования
пластических сдвигов продолжается в поверхностных слоях в
районе контура максимального контакта. При слиянии трещин
происходит типичное усталостное разрушение поверхностного
слоя металла. Доказано, что смазка в подшипниках качения облегчает
процесс разрушения за счет раскалывания образующихся трещин.
Первым актом , облегчающим разрушение твердого тела под влиянием
активной жидкости (смазочной среды), является ее проникновение
в устья микротрещины с вытеснением из них воздуха. Это проникновение
вызывается “всасывающим” капилярным давлением, достигающем
в весьма тонких зонах микротрещины при малых толщинах очень
высоких значений. Вторым актом действия среды при контактном
разрушении твердого тела является стремление к утолщению тонкой
смачивающей пленки жидкости ,проникшей в микротрещину. Наибольшие
давления расклинивания возникают в наиболее глубоких , тонких
частях микротрещины , куда только может проникнуть жидкая
пленка.
При применении КЕРАМИДОВ происходит вытеснение смазывающей
жидкости с поверхности, накатывается пленка, КЕРАМИД попадает
в трещину и частично ее заполняет. В результате высоких температур
в месте контакта обкатываемых поверхностей он изменяет свои
свойства превращаясь в материал подобный стеклокерамике имеющий
очень хорошие адгезивные свойства с металлом. Вследствие этого
происходит “залечивание” краев микротрещины, и существенное
уменьшение дальнейшего роста микротрещины. Скорость нагрева
поверхностных слоев в зоне контакта работающего подшипника
на несколько порядков превышают возможно достижимые при обычной
термической обработке и составляют соответственно 1 000 000
и 10 000 град/сек.
В результате вышеизложенного можно сделать
вывод о целесообразности применения составов типа КЕРАМИД,
существенно улучшающих технические параметры подшипников качения.
Многочисленные наблюдения за работой обработанных КЕРАМИДОМ
шариковых подшипников свидетельствует о четырехкратном увеличении
их срока службы
Условия работы зубчатых передач с КЕРАМИДАМИ.
Во время работы зубчатых передач в точке
зацепления имеет место перекатывание и скольжение зубьев.
Скорость относительного движения (скольжения) в точке контакта
пропорциональна расстоянию точки зацепления от полюса. В полюсе
она равна нулю , а при переходе через полюс меняет знак. Максимальное
значение скольжения наблюдается на ножках и головках зубьев,
на начальной окружности оно равно нулю и изменяет направление.
Скорость скольжения увеличивается с ростом высоты зуба и модуля
зацепления.
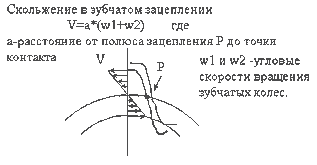
Трение является основной причиной потерь в зацеплении и износе
зубьев. Поэтому при уменьшении модуля зуба уменьшаются усталостные
выкрашивания зубов. Понижение модуля ограничивается способностью
зуба противодействовать его излому, т.к. при его понижении
уменьшается толщина ножки.
Сила трения одной зубчатой пары в коробке
передач автомобиля с мощностью двигателя около 50 квт равна
около 170 кг. Учитывая малые размеры пятна контакта, можно
сказать, что эта сила будет вызывать значительные контактные
напряжения.
Коэффициент трения в зубчатых передачах
изменяется от 0,06 до 0,1. Уменьшая коэффициент трения , который
при совместном использовании штатной смазки и КЕРАМИДОВ в
десять раз меньше, чем только при использовании штатной смазки,
можно добиться коэффициента полезного действия от зубчатой
передачи равного 99,2% на одну ступень. Обработка двухступенчатого
редуктора с КПД одной ступени 97% (КПД двух ступеней = 94%)
позволяет экономить 5% электроэнергии или топлива автомобиля.
Кроме того постоянное присутствие стеклокерамической пленки
на поверхности зубьев передачи, облегчает работу механизма
в начальный момент (момент пуска), когда масло на зубьях передачи
отсутствует. Пленка КЕРАМИДА противодействует заеданиям и
задирам, которые присущи быстроходным и высоконагруженным
передачам. В месте соприкосновения зубьев этих передач развивается
высокая температура, способствующая разрыву масляной пленки
и образованию металлического контакта, где происходит сваривание
частиц металла с последующим его отрывом от одной из поверхностей.
КЕРАМИД надежно устраняет сваривание, т.к. разрыв термоустойчивой
стеклокерамической пленки невозможен.
Применение КЕРАМИДОСОДЕРЖАЩИХ составов очень
эффективно с тяжелонагруженными тихоходными зубчатыми колесами
у которых очень часто наблюдается пластический сдвиг. При
перегрузках на поверхности зубьев появляются пластические
деформации с последующим сдвигом в направлении скольжения
(см. рис.). В результате у полюсной линии образуется хребет,
а у ведущего соответствующая канавка. Образование хребта нарушает
правильность зацепления и приводит к разрушению зубьев. В
таких случаях рекомендовали повышать твердость материала зубьев,
что ведет к удорожанию конструкции. Состав с КЕРАМИДАМИ одновременно
повышает прочность поверхности передачи и устраняет причину
сдвига - трение. Были попытки изготовить такие колеса из серого
чугуна методом литья. При износе чугуна выделялся графит,
который являлся сухой смазкой для зубьев колеса.
Сила трения совместно с силой от крутящего
момента вызывают переменные напряжения в течении длительного
срока, что вызывает усталостное разрушение поверхности зубьев.
В борьбе с таким видом разрушения особое значение имеют меры
по устранению концентраторов напряжения (рисок от обработки,
раковин и трещин отливках , микротрещин от термообработки).
Выкрашивание начинается обычно вблизи полюсной линии на ножках
зубьев там, где нагрузка передается одной парой зубьев. Это
справедливо как для прямозубых, так и для косозубых передач.
На поверхности зубьев появляются небольшие углубления, которые
потом растут и превращаются в раковины. При выкрашивании нарушаются
условия образования сплошной масляной пленки , появляется
металлический контакт с последующим быстрым износом и задиром
поверхности. Пленка КЕРАМИДА, при накатке, покрывает зоны
зубчатых колес в тех местах, где наибольшие контактные напряжения,
заполняя концентраторы напряжения и благодаря отличной адгезии
скрепляет кромки рисок и микротрещин, не давая им возможности
развиться в раковину. Высокая твердость доходящая до HRC 64
и термоустойчивость стеклокерамической пленки надежно защищает
поверхностный слой от выкрашивания. Повышение контактной прочности
поверхности зубчатых передач противодействует их приработке
(обкатке). Поэтому в некоторых случаях, когда зубчатые передачи
изготавливаются из сравнительно мягкого материала (HB<350)
необходимо перед обработкой выдержать срок необходимый для
приработки зубьев.
Уровень повышения твердости передач, подвергшихся
обработке КЕРАМИДАМИ, сравним с цементацией, с помощью которой
достигается поверхностная прочность 58-63 HRC. Как известно,
цементация это длительный и дорогостоящий процесс.
После цементации форма зуба искажается ,
а поэтому необходима последующая обработка с доводкой формы
зубьев до нормальной. Применение КЕРАМИДОВ для упрочнения
зубьев очень простая и не требует длительных остановок оборудования
и тем более последующей обработки.
При работе зубчатых передач вследствие деформации валов, корпусов,
опор и самих зубчатых передач, а также неизбежных погрешностей
в изготовлении и монтаже, создаются в зацеплении дополнительные
динамические нагрузки, а полезная нагрузка распределяется
не равномерно по длине зуба. Поправочный коэффициент рекомендуется
выбирать для прирабатывающихся передач = 1,3 - 1,5 , а для
не прирабатывающихся = 1,5-2,1. Этим подтверждается , что
реально пятно контакта в редукторах иногда может быть более
чем в два раза меньше идеального. Это приводит к сильным динамическим
нагрузкам, вибрации и шуму. Применение КЕРАМИДОВ позволяет
за счет накатки избавиться некоторых дефектов: а) повышается
эквивалентная чистота обработки поверхности зубьев; б) накатка
состава происходит неравномерно в результате чего выбираются
излишние зазоры; в) происходит «закатывание» раковин. Проведенные
измерения шума редукторов до обработки и после показывают
уменьшение его на 5 - 7 децибел (1,8 - 2,2) раза. Происходит
уменьшение виброускорений на 10 - 15 %. Т.е. зубчатые передачи
работают более плавно, что также влияет на их долговечность.
Практика показывает, что после обработки составами с КЕРАМИДАМИ
уровни масла в редукторах можно снизить до такого уровня при
котором возможно только минимальное касание одного из колес
масла.
В некоторых случаях возможно применение редукторов
без масла. В таком случае они работают по срокам до отказа
такое же время, как и не обработанные со штатной смазкой.
При работе без смазки полностью убираются гидравлические потери
, что особенно важно при работе механизмов в условиях низких
температур. Отсутствие смазки важно при работе открытых зубчатых
передач в условиях сильной запыленности.
В червячных редукторах червяк скользит по
зубьям колеса как в винтовой паре. В следствие этого смазка
приобретает особое значение. Кроме смазывания рабочих деталей
она еще и охлаждает их. Коэффициент трения в червячных передачах
зависит не только от материала деталей и чистоты их обработки,
но и от скорости его вращения. Он изменяется от 0,12 до 0,02
при скоростях скольжения от 0,01 до 15 м/сек. Вследствие этого
коэффициент полезного действия червячных передач низкий и
составляет 0,7 - 0,9. Потери происходят из-за высокого трения,
вызывая нагревание редуктора. При обработке червячного редуктора
КЕРАМИД внедряется в тело более мягкого металла. И только
после его превращения в стеклокерамическую пленку, имеющую
повышенную прочность, происходит внедрение в более прочный
металл. После обработки червячных редукторов всегда понижается
их температура, и как следствие уменьшения трения увеличивается
КПД. Проведенные испытания подтверждают эффективность применения
КЕРАМИДОВ для червячных передач. Высокооборотные червячные
передачи работают длительные сроки (до года) без жидкой смазки
«насухо» с пониженной температурой корпуса.
Применение составов типа КЕРАМИД в зубчатых
передачах позволяет:
а) Увеличить коэффициент полезного действия
передачи;
б) Отказаться от дорогостоящих методов термической
обработки;
в) Уменьшить или отказаться от смазки маслом;
г) Увеличить плавность работы передач и уменьшить
ее шумы;
д) Исключить задиры и заедания;
е) Увеличить контактную прочность зубьев,
что исключит их выкрашивание;
ж) Уменьшить гидравлические потери при низких
температурах;
з) Увеличить передаваемую мощность на редукторах
одинаковых габаритов;
и) Исключить аварийные простои оборудования
содержащего зубчатые передачи;
к) Продлить втрое срок службы редукторов
и коробок передач.
|